Project - Project Participants
The Business of Haussmann is to plan and commission HML M3 Building Systems Manufacturing Plants
- Plant design
- Plant establishments
- Taking plants into full production
- Plant ownership
- Appoint and handover each plant to a nominated plant management company for a term of up to 23 years per plant, to manage each plant on behalf of Haussmann Limited.
Bromelton Plant Infrastructure
Planning | Timetable & Sequence |
Funding | Timetable & Sequence |
Project Agreements | Timetable & Sequence |
Corporate Entity 1 – 2022
One off Pilot Production
to produce building systems to achieve Australian Standards Approvals for non-Structural building systems). This Investment is offered as a mitigated investment – a Property secured investment. AUD $3.8 million
a HML – mitigated, property secured Investment offer – for (Sophisticated Investor(s)
Plant Engineering Agreement 1. Planning, Preparations and production Management by Coordinating Engineering Agreement 1 2022
Corporate Entity 2 – 2022
Haussmann Waste Management & Transfer Station
Project Management – Agreement 2. pre Planning preparations by Coordinating Engineering Agreement 2 – appointed Project Management Group 2022 – 2023
Corporate Entity 3 – 2022
20 Display homes “marketing tools” – to start pre-sales of single dwellings/residential homes – marketing programmes, when Display homes have been build. This Investment is offered as a mitigated investment, a Property secured investment AUD $26 million
a HML – mitigated, property and improvements secured investment offer – for (Sophisticated Investor(s).
Build by Haussmann – Builder’s Lic. 182320C – Assembly and installations Division: Contract 1 2022
Corporate Entity 4 – 2022
Incorporation of SPV 1 – Special Purpose Vehicle – Bromelton (SDA) Plant infrastructure preparation and plant establishment management entity Investment preparations costs # AUD $75 million HML to appoint SPV Management Team. (Commercial Manager – nominated to manage SPV 1 Team). 2022 – 2023
Funding Raised via Crowd Funding – initial Australian funding program AUD $ 5 million funding program for Retail Investors, minimum Investment per Investor: $10 K, maximum investment $20 K. 2022
IPO (initial Public Offering) Haussmann Limited Listing – Listing and fund raising Programs: AUD $ 5 million 2022
Funding Programs via Equity Crowd Funding Platforms (Global Programs) 2022-2023
Major Accounting Firm (initial discussions with PWC to prepare HML Project funding Submission to Qld. State Development. (on completion of Bromelton HML Plant infrastructure Master Plan). HML convertible Bond issue preparations. 2022
Independent Project Auditor Via SPV 1 – Appointment 2022
Commercial Manager Via SPV 1 – Appointment – nominated to manage SPV 1 Team. 2022 – 2023
Project Management Group Via SPV 1 – Appointment to prepare Master Plan for Bromelton Plant infrastructure establishment – Project Management Agreement 1. 2022 -2023
Project Management Group to prepare Plant infrastructure design – planning approval processes for the establishment of HML Plant at Bromelton. Project Management Agreement 3 2022 – 2023
Coordinating Engineers appointed. Task 1: Identify 3 Plant Engineering Groups, capable to provide blueprint for all engineered Plant production reference: HML Generic Plant design sections, Building 1 and Building 2, identify suitable suppliers for machinery and Equipment
Civil Engineering and Construction Via SPV 1 – Project Management Group / Procurement Group –HML M3 Building Systems Manufacturing Plant – Bromelton (SDA) Infrastructure Project Management Agreement 4 2022 -2023
Plant Engineering Group Via SPV 1 – Appointment (Germany) to prepare and complete Plant Blueprint – Plant Engineering Agreement 2 2022
Procurement Group Via SPV 1 – Appointment – Multi-pronged Procurement Programs – supply of goods and services for: A: Plant establishment, B: Plant Production 2022
Haussmann – Builder’s Licence 182320C – Via SPV – Appointment – HML Home assembly and installations Division – 2022 -2023
HML – SPV 1 Project Management
Click image to enlarge
Project participants
Project Management: Nominated – appointed
Procurement: Management Options Pty Ltd – appointed
Coordinating Engineers: Projectus Infrastructure Services – appointed
Plant Engineering: Nominated – to be appointed
Technical Auditors: to be appointed
Patent Attorneys: Dark IP – appointed
Legal Adviser: Equius Legal Pty Limited – appointed
Corporate Adviser: Nominated to be appointed
Stockbroking Firm/Securities Dealer: To be appointed
Equity Crowd Funding Platform (Australia): – appointed
Digital Content Marketing: appointed
Grant Consultants: Intertrade Advisers Pty. Ltd. – appointed
Accountants: Mosman Accountants (5stargreen Building Technology Trust) – appointed
Project insurance Consultant: Austcover Pty. Ltd. – appointed
Technical Auditor: To be appointed
Management Contract: Haussmann SPV 1 Pty. Ltd. – (Special Purpose Vehicle Management Co.) – incorporated
Home installation Project Management: Ultimate Builder Pty. Ltd. – appointed
Power Plant establishment – Consulting Advisers: BOC – Linde or ThyssenKrupp Australia – nominated to be appointed
Gas Pipeline Contractor: – nominated – to be appointed
HML Plant:
Management Contract: Heavy Engineering – to be appointed
Management Contract: Aluminium Extrusion – Doors, Windows –fabrication – to be appointed
Management Contract: Container Fabrication – to be appointed
Management Contract: Kitchen – Bathroom – fabrication / assembly – to be appointed
Management Contract: Thermo- syntetic solid surface production – appointed
Management Contract – Plant Management: To be appointed
Reference: Content 1
Click on image to enlarge
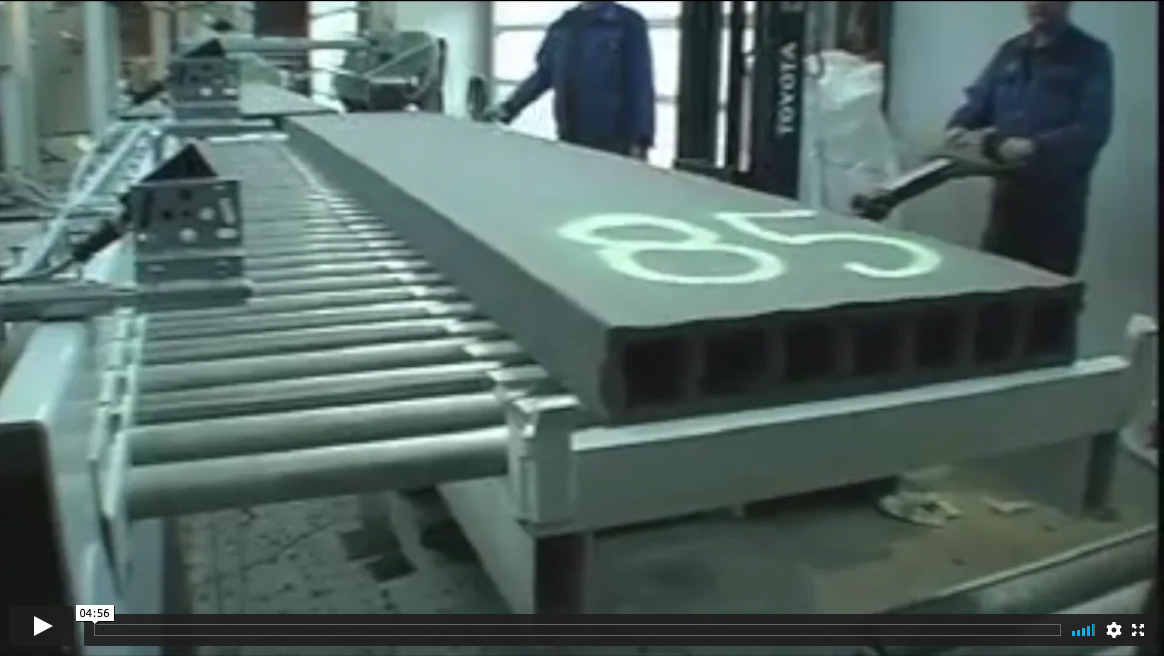
Green, Sustainable Housing For All
Carbon Credits……. Co2 Emissions elimination…….how is it achieved ?
Haussmann has developed building systems consisting of unique connections and joining methods and panel systems in various sizes and designs (Haussmann M3 housing systems panel designs make it possible, to design and build any size home and any configuration of space, within a single dwelling and or range of dwellings).
Residential housing, the way it is presently being built, and on-site building methods, are major contributors to greenhouse gas emissions, with most emissions being generated during the operation of wet building the residential dwelling on site.
The Haussmann manufacturing processes will eliminate such emissions, by dry building such residential dwellings, as each Haussmann home is built in controlled factory conditions. (No emissions)
We are confident that we can offset our substantial carbon credits with our nominated provider of cement and other providers of goods and services impacting the environment and achieve an overall advantage of pricing/purchase of goods and services benefits.
Before Haussmann carbon trading, HML will have its carbon credits certified to “standards” https://www.goldstandard.org, https://cdm.unfccc.int
The Haussmann Building Systems, a sustainable, green and affordable building System...
Haussmann M3-dimensional box space systems are the main building elements of its systems. “Box units” contain application engineered composite materials panel systems consisting of floor panels, wall panels, and ceiling panels and or divisional panels are assembled on-site. They contain finished works, wall, ceiling, and floor finishes, electrical wiring, freshwater piping, and wastewater and sewerage pipe, ducted air conditioning and intelligent wiring.
The size of the three-dimensional modules and location to each other, are determined by client design. The length is limited due to weight constraints to 6.00 – 10.00 meters. The resulting weight of 300 – 400 kN is within the limit of what heavy mobile cranes can handle at the maximum reach required for erection, lighter weight, application engineered composite panel constructions, like roof panels, for example, which can be slightly larger and longer. Haussmann industrial construction methods are compliant and will perform to physical performance, stability, strength, thermal and acoustic requirements, maintainability and insulation, aesthetics, functionality, versatility, and flexibility.
New materials and production methods include connecting, jointing and finishing techniques. Plant blueprint designs assure implementation “by the book” planning and coordination of production, quality control, transportation, and construction. Extensive analytical and marketing studies have been carried out on the Haussmann range of products; forecast on demands; scope and characteristics; and selection of the most profitable method of production and optimal locations and size of the production plant in accordance with demand within a designated “catchment”/area. Feasibility studies have covered marketing, advertising, sales/design/graphic engineering and motion graphic modelling to enable client choice, including first mortgage in-house financing for every client/customer ($2 first mortgage deposit, Term up to 30 years, interest rate fixed at 5 % p.a.). We are confident that both Bond issues will sell well. Social Capital is a great capital offering for global enterprises like Haussmann.
HML’s Definition of
Intermingled raw materials
Mixed solid waste
A green and sustainable – renewable
Raw Materials Source
Categories of mixed solid Waste
Building & Demolition | Concrete and other building rubble, asphalt, mortar, bricks, tiles, masonry, excavated earth, sand, rip rock, sandstone, marble, slate, granite, glass, cement render, clay pipes, ash |
Wood (all) | Furniture & bedding, timber pallets, doors, man made timbers, flooring, all structural timbers, ceilings, cladding, tree trunks and roots, crates, combustibles, garden waste, paper board, construction paper and board, wallboards. |
Glass (all) | All kinds of glass. |
Metals (all) | Plumbing, steel, ferrous and non ferrous metals, baths, vanities, lights, kitchen fittings, cladding external and internal, air conditioning and ducts, electrical wires, plant and fittings, gutters, down pipes, aluminum frames, drums, casting alloys, wrought aluminum and iron, copper, brass mill products, bronze products, wire and wire products, lead, zinc, galvanized products, nickel, stainless steel, steel rolled products, precious metals. |
Textiles (all) | Waste clothing cuts, wool and textile mix synthetic carpets. |
Paper (all) | Cardboard, newspapers, magazines, packaging and all paper-based products. |
Mixed Rubble | Material handling items, transportation items, gypsum, textiles, carpets and floor coverings, padding, fillers and wipers, plastic films, wrapping materials, card¬board on internal walls and ceilings, tiles, plasterboard, vinyl sheets and tiles. |
Plastics (all) | Electrical items, home wares, various appliances and equipment, plastic polyolefin (high- and low-density polyethylene and polypropylene), polystyrene, polyvinyl chloride (PVC) Polyethylene (PE), thermoplastics, thermosets, all packaging. |
Rubber (all) | Appliances, footwear & items of clothing, marine items, tires, rubber products and fittings |
Gross Waste Received | (t/p.a.,) This line records the expected tonnage of waste to be received by the Plant each year. This is a Gross Tonnage of 750000 tones. |
Unwanted Waste | (as % of Gross) This is an engineering provision to downgrade the production efficiency of the plant. There is a consistent provision of 5 % and this includes provision for shrinkage during the drying process of various categories of waste such as green trees, wet paper and so on. |
Acceptable Waste | This is Gross Waste less than 5%. The Plant takes 712,500 tones of raw material into production. |
Growth in acceptance | This is an allowance for efficiency improvement in years to come. Set at 3% for the purposes of planning. |
Truck capacity cubic m2 | This is required to enable complete assessment of the space requirements. In this plan containers on trucks (20-foot) are assessed to have capacity of 27.9m3. |
Number of truck trips | This is calculated (p.a.) by converting the Gross Tonnage of Waste received annually into cubic meters (volume) and dividing it by 27.9 m3 the latter being the “Container capacity in cubic meters”. In this plan there are in excess of 120 – 150,000 container movements to the Bromelton HML Plant annually. |
No. of trucks p. day | This is calculated by dividing the annual number of trucks with net plant production working days per annum (280 net production working days per annum). There are 536 by 20-foot containers coming into the plant every day delivering compacted waste. |
Reference: Content 2
Transfer Station: Waste Stream Provisions for Bromelton Plant
10 Year network program upgrades for Transport and Infrastructure
https://www.infrastructureaustralia.gov.au/map/brisbane-gold-coast-transport-corridor-upgrades
Gold Coast Light Rail Stage 3A (Priority Project)
M1 Pacific Motorway – Eight Mile Plains to Daisy Hill (Priority Project)
M1 Pacific Motorway – Varsity Lakes to Tugun (Priority Project)
M1 Pacific Motorway between Eight Mile Plains and Tugun (High Priority Initiative)
Gold Coast Rail Line capacity improvement – Kuraby to Beenleigh (Priority Initiative).
Compacted waste in 20-foot containers, cost effective, can be transported by large trucks from Transfer Station to HML Bromelton Plant. Container size: (6.06 meters x 2.44 meters x 2.59 meters) Weight each container: 2,220 kg
Waste Management company operation:
HML Waste Bin collection trucks collect mixed solid waste from industrial and commercial sources.
Waste from further afield, e.g. Central/North Qld/Darling Downs could be containerised and railed as part of regular intermodal operations direct to Bromelton for processing as would waste from interstate (this could also be shipped through PoB and then railed to Bromelton ( $ 60 per tone).
Mixed solid waste sources from industry and commercial waste producers, will come from the greater area of Brisbane and the Gold Coast within a radius of up to 80 km from nominated waste management company location.
Cost Estimates:
A.) Approved Land area: $ 5 – 20 million
B.) Buildings and internal Roads and Hardstands $ 8 million
C.) Machinery and Equipment, Trucks, Bins $ 12 million
D.) Lease / Purchase cost $ 10 million over a 60 months period
1.) Haussmann Plant Waste Management Company location,
2.) should be located in the southern Corridor,
3.) halfway between Brisbane and the Gold Coast,
4.) where waste is accepted and compacted into containers,
5.) moved by Road transport – 20-foot containers – to HML Bromelton Plant.
A.) Required Space/Areas: Total 110 000 square meters
Truck parking area 16 000 square meters
Bin storage area 32 000 square meters
Container hard stand (empty Containers) 15 000 square meters
Container hard stand (full Containers) 15 000 square meters
B.) Transfer Station (roof covered are): 16 000 square meters product being unloaded from collection Bins (all sizes)
2 level operation- unloading waste from bins onto conveyor, conveyor feeding waste into compactor
Compactor pushing, compacting waste into containers.
C.) Site Office Building
D.) Weigh Bridge
E.) Container Hardstand (1 and 2) for outgoing (loaded) and empty containers (to be loaded).
F.) Land area required: Total 110 000 square meters
G.) Type of Zoning required (and or to be obtained) if greenfield – cost per square meter from $ 50 to $ 200
Medium impact zone approval ready to build – $ $ 250 to $ 280 per square meter.
(Road must be approved for V-Doub Trucks).
F.) Number of Container Movements per annum:
Movements of up to 120 – 150.000 – 20-foot containers are required to provide the plant’s feedstock of mixed solid waste per annum.
Accordingly, a logistics/movement model of number of containers, (empty container – hardstand)
hardstand (filled containers with waste – hardstand) is required.
New Materials made possible via new Materials Technologies are the Key to industrialisation of Production for Buildings and a new way of building. (Finished Product outlines and Comparisons).
Total changes and radical improvements of productivity, quality and price in building construction can only be attained through new materials and intensive industrialisation and full automation of the total building/housing process. Building materials are generally viewed as a high-weight, low-value product. Haussmann panels are a low weight, high volume product and therefore a low-priced building material. Haussmann and the BTT will continue to maintain its cutting-edge market position by spending fixed allocations of funds on research and development. It will continue to identify new technologies that add synergy to the existing business and help add shareholder value. There are currently no other comparable building products on the market in terms of cost, quality and quantity.
Our focus on implementing new materials and technology processes will instigate deep social changes. The most important task of the technology progress undertaken by Haussmann in building, is therefore to increase the extent of industrialisation, with a view to total automation, wherever feasible (Cubic meter (M3) building systems by Haussmann).
Haussmann’s use of computer digital tools in design and robotics in the manufacturing and production of all building elements used, gives Haussmann’s new methods a massive competitive edge locally and globally.
Using economics of scale, our mass production, capital investment into manufacturing facilities and management and auxiliary services are to be located in central locations, which will make shipping and/or other means of transport to various consumer areas most cost effective.
Competition for Haussmann Housing Systems is simply non-existent. Currently, there are no competitive equivalents, in terms of affordability, volume generation and quality on the market.
There may be, by self-appointment, several competitors, however, when compared to the Haussmann high quality products, there is no real competition. The Haussmann Manufacturing System provides application engineered products which are fully integrated and flexible products that outperform all other building materials and panel systems currently on the market.
No other products can be delivered in a similar or same manner as our Products. Our application engineered panels are far ahead of competitor panels and traditional construction methods and materials. The revolutionary nature of the Haussmann Panels means that traditional building materials will potentially be seen as obsolete. Haussmann “construction contract” on site dwelling establishment, guarantees to build any average size home to lock up stage within weeks or less, ready for the customer to move in (agreed date of completed building handover to customer).
Centralised industrial volume production. Our centralised high-volume production and work teams within a sophisticated industrial organisation, is capable of high quality of planning, coordination and control functions with respect to production and distribution of its range of products.
To ensure optimal organisational results of production, a very high degree of coordination exists between design production and marketing of our range of products. Our integrated systems ensure in a most effective way, that all functions are performed under a unified central management authority. This applies to the establishment of any Haussmann plant and the operations of any Haussmann plant globally.
Our industrial, automated features in both design and the production of products, makes the overall proficiency of workers in execution of individual task less strenuous (trained labour). Haussmann’s sophisticated production tools and in part, robotic production controls, shifts the emphasis from worker specialisation in individual activities to their understanding of the total process and its underlying technologies. This applies to both controlled factory areas of production and housing systems installations on site (executed techniques and procedures).
Our housing systems’ technologies and designs provides clients with a choice of 3 standard sizes: small, medium or large m3 (cubic-meter) sections, which can be arranged, interconnected and interchanged as per the client’s design. All components are modular so almost any size arrangement of M3 panels / housing systems and spaces, doors and windows and service pods are possible. All individual housing designs, as per customer’s order, instructions, finishes and configurations are designed by each and every Haussmann customer.
Haussmann has mastered the challenge of industrialisation in building, from architectural, technological and industrial mass production (21 million m2 panel production, per plant p.a.) quality, in standardising its new building components and ensuring maximum design freedom with respect to the final building product (A Haussmann Home). Present methods of building, carried out by builders, are basic and simple, archaic and clunky methods of building, compared to Haussmann buildings, which are precision engineered, engineered in and under controlled conditions, factory finished, exceptional quality finished, precision engineered buildings.
New production techniques employing computer-aided, digital designs and manufacturing permits considerable diversification of output without affecting construction feasibility. The system has dispersed across most of the onsite construction activities. Infrastructure, part foundations, erection and finishing components are carried out off-site at Haussmann’s centralised manufacturing plant facilities, providing substantial product core and high-quality finishing benefits achieved by better machinery and production equipment and overall organisation.
Conventional building site work environments and the physical hardship of construction work in rugged conditions have been eliminated by the Haussmann building systems. All parts of construction work are now performed in a Haussmann plant, which is a hospitable industrial and effective workplace (Dry building methods).
Benefits and merits of Haussmann automated housing systems’ realisation, which employs automation in the production of building elements in the manufacturing and prefabrication plant require minimal time for remaining on-site erection works.
Industrialisation, mechanisation and automation of the building industry will save manual labour and eliminate strenuous, dirty and dangerous work, resulting in flexibility and improvement of quality overall. Haussmann uses computer software systems for analysis of the performance of its various buildings systems and composites of the elements, structural, mechanical and environmental, checking that they conform to accepted codes and standards. Independent tests of composite materials variations have been carried out by independent testing institutions in Europe.
Conventional construction methods versus the Haussmann industrial mass production – systems and superior range of housing products.
A conventional construction process involves 20 to 30 different skilled trades. This complexity is caused by the multitude of functions. A typical building must provide shelter, adaptable thermal and acoustic conditions, locomotion between different areas and levels, water and power supplies, disposal of wastes, illumination, communications with the outside world and specific functions, within particular spaces for cooking, recreation, storage, sports activities and other various processes.
Those proliferations of functions and large number of works coordinated and adapted to each other have been eliminated by the Haussmann manufacturing process, by combined comprehensive assembly adapted to their comprehensive multipurpose functions.
Haussmann’s far-reaching solutions under the principal of producing all parts for assembly of a whole building, and its sizable parts, with all its necessary finishes and works are completed in a Haussmann plant, which makes the transportation and erection process a simple and time effective undertaking (Haussmann home finished to lock up stage within days).
Our building systems products are guaranteed for 50 years plus, but the actual service life may be much longer. Building life cycle implications with regard to several aspects of building performance is quality, which is of paramount importance and which is insured by design and control during in-plant production.
Our flexible building cube M3 structures are designed to be adapted to the dynamics of family growth, change of lifestyle and living standards; without modification of components, or changing of user requirements or special maintenance needs or making living spaces smaller or bigger.
The distinctive nature of every building project, for its procurement process and individual inputs, act independently from each other, sponsor, designer, contractor etc. – this divided authority reduces overall efficiency. Haussmann integrated systems have done away with the distinctive nature of “one off”, boutique building. Every building project and in a most effective manner, superbly enhances user needs and creates new market conditions, and as such, provides superb entrepreneurial attractive alternatives to create an unlimited market for its products globally.
Trade increases will be stimulated by stricter environmental and land use regulations, continuing improvements in mining, processing and material handling technologies (making production and shipping operations more efficient). Further expansion of coastal and offshore sources of supply, (lower water-based transportation costs, allowing product to be shipped greater distances) and the response to development of spot shortages means high-growth markets.
The building systems can be defined as a set of interrelated elements that act together to enable the designated performance of a building. It also includes various procedures and technologies, processes and designs and new materials technologies and composites, for the production and assembling of these elements for this purpose.
Our housing designs, productions and erection on-site, are strongly interrelated and are parts of integrated process, which reduces human involvement, improves quality of design, production and on-site installations.
Benefits of industrialised Haussmann building systems include saving of on-site labour, elimination of skilled labour, a substantially faster construction process and earlier completion and substantially higher quality of components due to better production “tools” and quality control.
Our benefits are realised and provide large economic gains to our clients, due to substantially lower costs of new materials (use and processing of intermingled raw materials – mixed solid waste). Every Haussmann home, when established, for and on behalf of its customer, will immediately increase in value by 50%, to match existing housing market values as applied and dictated by market forces. The automated design and production procedures allow for the use of custom-made components for each individual project without additional costs, and at the same time provide an abundance and variety of shapes and finishes. We developed a building system consisting of unique connections and joining methods and panel systems sizes and designs.
Our building system has done away with one of the greatest impediments to constructing a building: the professional builder and his or her crew, the architect, the quantity surveyor, complex DA and BA approval methods. Industrial construction methods are compliant and will perform to physical performance, stability, strength, thermal and acoustic requirements, maintainability and insulation, aesthetics, functionality, versatility and flexibility. This is all made possible by Haussmann’s new materials, production methods, connecting, jointing and finishing techniques.
On behalf of the home purchaser, pre-DA and BA approved plant blueprint housing systems designs assure implementation “by the book” planning and coordination of production, quality control, transportation and erecting.
Each conventional single dwelling is made up of a number of M3 spaces, such as bedrooms, dining room, bathrooms, garages, storage rooms, general recreational areas etc. Haussmann three-dimensional box space systems are the main building elements of its systems and can be totally free – span by space design.
Box units are made up/connected of application engineered composite materials panel systems, consisting of floor panel, wall panel and sealing panel, divisional panels and roof panels, and are assembled (clicked together) on-site. They contain finished works, wall, sealing and floor finishes, electrical wiring, freshwater piping and wastewater and sewerage pipe, air conditioning ducts and intelligent wiring. The size of the three-dimensional modules, designed and by position location to each other, are determined by client. The length is limited due to weight constraints to 6-meter lengths. The resulting weight of 300 – 400 kN is within the limit of what heavy mobile cranes can handle at the maximum reach required for erection, lighter weight, application engineered composite panels, like roof panels for example.
Three-dimensional modules contain all finished works; such systems, when employed, function better than any other systems. The ultimate objective of industrialisation is the maximum of savings on the individual and is in part, due to no professional labour on site and precision engineered “parts”. Three-dimensional box space systems provide friendly and client compliant building layouts, which can be effectively portioned and/or connected to any other box space and are much more flexible than linear or even planar elements.
3D box space designs, consisting of inter-connected application engineered composite building systems, are lightweight, easy to install and are ready for customers to move in, once all “space boxes” are installed. Typical home M3 sections/spaces are kitchen, bedrooms, bathrooms, toilets, garages, including non-specific living spaces, like an office, baby’s nursery, home theatre and/or men cave etc. Each HM client/customer can design his or her home spaces by mixing and inter-blending any size m3 configurations, sizes and 3D finishes, for a final configuration of his or her home choice.
Haussmann housing space boxes in checker board fashion, can be stacked as a 2 story building and built on a Haussmann 1.20 x 1.20 floor grid single post steel system, which provides the space boxes with structural support for height and pattern of a 2-story building.
To become a preferred Haussmann homeowner and be in receipt of a priority allocation option or for the purchase of a Haussmann home (as per customer design), one simply becomes a Haussmann investor. Any Haussmann investor minimum US$10000.00 will receive the same amount invested into Haussmann equity, as a bonus Haussmann home deposit allocation, with the priority right to purchase a Haussmann home. Terms and conditions within an agreed contract term, for a specific size home, to an agreed price, period and right of exercisable purchase option apply.
Global population growth, natural disasters, wars and the constantly increasing economic development of countries such as China and India equate to more waste generation and the need for construction of energy efficient, low cost housing, (particularly as populations urbanise). This statement of facts can only benefit Haussmann in the future. Another factor promoting the growth of the company is the increasing number of individuals, groups and companies that believe in the future of “green” (environmentally sustainable) and socially beneficial technologies.
Haussmann will appeal to these parties with its developed systems. Haussmann will aid and alleviate two major global problems: chronic housing shortages and waste disposal. The Haussmann building systems’ factors will appeal to the building materials market, which has been seeking a suitable low-cost product to replace the increasingly expensive and environmentally unsustainable building materials currently in use. Haussmann housing and panel systems and materials are the only range of products able to meet such local and global demand when in production.
Reference: Content 3